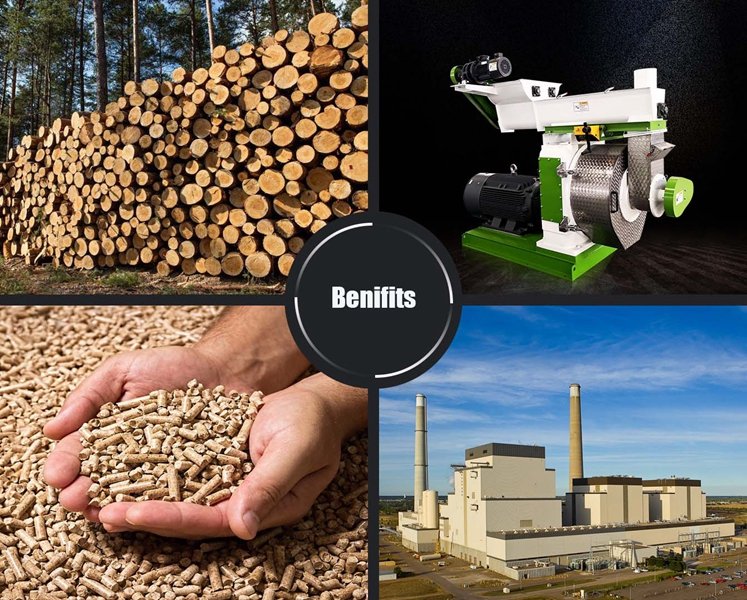
Introduction to Wood Pellet Machines
Wood pellet machines are essential in the biomass industry, facilitating the conversion of raw organic materials into sustainable fuel sources. The primary function of these machines is to compress sawdust and wood shavings into small cylindrical pellets. The quality of the final product heavily relies on numerous factors, one of which is the design and functionality of the ring molds used during the pelletizing process.
Ring molds play a crucial role in determining the density and durability of the wood pellets produced. They function by providing a confined space where wood particles are compressed under high pressure and temperature, resulting in a solidified form that efficiently burns as fuel. The design of these molds can vary significantly, affecting the flow and compaction of the material. A well-designed ring mold can enhance the efficiency of the wood pellet machine, leading to improved throughput and quality of pellets.
The interrelationship between machine design and pellet quality is a pivotal element in pellet production. The specifications of the ring mold, such as hole diameter, thickness, and material composition, directly influence the size, uniformity, and burning properties of the pellets. Different wood pellet machines may employ unique designs that cater to specific types of raw materials or production rates. For instance, the density of the ring mold material itself is crucial; stronger materials tend to yield higher quality pellets with less wear and tear over extended production runs.
Understanding these fundamental aspects of wood pellet machines and the significance of ring molds establishes a foundation for further exploration. It also allows for a clearer examination of various case studies that illustrate the technical challenges and solutions encountered in the effective operation of wood pellet machines, particularly those utilizing ring molds.
Case Study 1: 1-5 Tons/Hour Production
The implementation of a wood pellet machine with a production capacity ranging from 1 to 5 tons per hour presents several technical challenges that must be addressed during the installation and operational phases. One of the foremost issues encountered was equipment calibration, a critical process that ensures the machine operates efficiently and produces pellets of consistent quality. Initially, the calibration of the wood pellet machine was not aligned with the specific characteristics of the raw materials being used, which in this case included sawdust and wood shavings. This misalignment hindered the machine’s efficiency, resulting in varied pellet densities and imperfections.
Furthermore, material handling posed another significant challenge. The design of the feed system was inadequately suited to manage the volume and variability of the raw materials. Blockages and uneven material flow were frequently observed, leading to production downtimes. To rectify these problems, an assessment of the feed system was conducted. Modifications were made to enhance the material flow by optimizing the feeder’s speed and adjusting the angle of the feed chute. Additionally, training was provided to operational staff to improve their handling techniques, ensuring proper loading of raw materials into the machine.
Another technical challenge arose from the moisture content of the raw materials. Wood pellets require a specific moisture range to form correctly. It was discovered that the moisture levels in the wood materials fluctuated significantly, which impacted the pelletizing process. To mitigate this issue, a moisture analysis system was integrated with the wood pellet machine, allowing continuous monitoring and adjustment of moisture levels in real-time. As a result, these strategic modifications led to a substantial increase in productivity and a marked improvement in pellet quality, establishing a foundation for future operations.
Case Study 2: 10-15 Tons/Hour Production
The implementation of a wood pellet machine with a production capacity of 10-15 tons per hour presents unique challenges, particularly concerning feedstock variations. Various types of biomass, such as wood shavings, agricultural residues, and sawdust, can differ significantly in moisture content, particle size, and density. These discrepancies can adversely affect the final pellet quality, impacting both density and durability, which are critical parameters for successful pelletizing.
In this case study, we encountered notable issues with pellet density due to inconsistent feedstock quality. The variations in material directly influenced the compaction process within the wood pellet machine, leading to an uneven distribution of pressure exerted during pelleting. To address these challenges, technical adjustments were made to optimize the ring mold diameter as well as roller speed settings. By refining the ring mold diameter, we were able to enhance the compression ratio, which is vital for achieving denser pellets.
Additionally, adjusting the roller speed proved essential in maintaining a consistent output quality. Higher speeds can lead to increased friction and heat, which may cause excessive wear on the machinery and affect the integrity of the pellets. Conversely, too low a speed can impact the rate of production. Through careful monitoring and real-time adjustments, a balance was struck that not only increased the overall efficiency of the wood pellet machine but also improved the durability of the final product.
Ultimately, the successful optimization of these parameters has resulted in a robust solution for producing high-quality wood pellets, despite the initial challenges posed by feedstock variation. This case study underscores the importance of adaptive strategies in achieving consistent outcomes in biomass pelleting, demonstrating that meticulous attention to detail and proactive adjustment are essential for operational success.
Case Study 3: 20-25 Tons/Hour Production
In the endeavor to produce wood pellets at a capacity ranging between 20 to 25 tons per hour, several technical challenges emerged, particularly concerning the maintenance of machine temperature control. The wood pellet machine operates under specific thermal conditions that significantly impact the characteristics of the biomass being processed. When the temperature within the machine exceeds the optimal range, it can lead to undesirable alterations in pellet quality, such as reduced durability and inconsistent density. This phenomenon highlights the critical nature of effective temperature management in the wood pellet production process.
One significant challenge faced was the overheating of components within the wood pellet machine during high-capacity operation. Such overheating not only compromises the performance of the machinery but also degrades the biomass material. To address this, enhancements to the cooling system were implemented. The introduction of more efficient cooling mechanisms, such as improved air circulation and water cooling systems, played a pivotal role in maintaining the temperature within acceptable limits. By effectively dissipating heat, it ensured that the materials processed retained their integrity throughout the manufacturing cycle.
Additionally, adjustments to lubrication methods proved to be crucial in maintaining optimal operation. Proper lubrication is vital in reducing friction and wear, which can otherwise lead to increased temperatures in the wood pellet machine. The project team explored advanced lubricants designed to withstand high temperatures while providing effective protection to the machinery’s moving parts. This adjustment not only helped in maintaining the machine’s efficiency during extensive use but also contributed to extending the lifespan of the equipment.
Through the implementation of enhanced cooling systems and optimized lubrication methods, the challenges posed by temperature control were effectively managed. This case study exemplifies how attention to technical details can significantly improve the overall performance of a wood pellet machine, ensuring stability in production and quality throughout the manufacturing process.
Case Study 4: 30-35 Tons/Hour Production
The implementation of a high-capacity wood pellet production line capable of processing 30-35 tons per hour necessitated a thorough evaluation of its operational efficiency and output quality. A primary concern raised during this assessment was the issue of pellet expansion, which directly impacts both the quality and the usability of the final product. In instances where pellets expanded excessively, it indicated deficiencies during the conditioning phase, which is critical for moisture and temperature regulation before pelleting.
To address these challenges, modifications were made to the conditioning stage of the production process. By optimizing the temperature and moisture content of the raw materials, it became possible to create a more favorable environment for efficient pelleting. The introduction of advanced monitoring systems allowed for real-time adjustments to the conditioning parameters, ensuring that materials were at their optimal state prior to being formed into pellets. This proactive approach significantly reduced problems associated with pellet expansion.
Another issue that emerged was related to the wear of ring molds, which can deteriorate over time due to the high pressures involved in the wood pelleting process. To combat this problem, durable materials specifically designed to withstand such conditions were utilized in the manufacturing of the ring molds. This strategic modification extended the lifespan of the equipment and maintained the production of high-quality pellets, thereby mitigating downtime and increasing overall operational efficiency.
By implementing these solutions, the wood pellet machine line not only achieved its production targets but also maintained stringent quality control measures. The combination of these advancements has led to significant improvements in product performance, ensuring that the final output meets industry standards and client expectations. Ultimately, addressing these technical challenges has set a precedent for future projects involving high-capacity wood pellet production.
Case Study 5: 35-40 Tons/Hour Production
In the context of a wood pellet machine project designed for a production capacity of 35-40 tons per hour, several technical challenges emerged, notably concerning the high-pressure build-up within the compression chamber during the pelletizing process. This situation posed significant risks, including potential equipment failure and decreased operational efficiency, thereby necessitating an in-depth examination of the machine’s design and component selection.
The initial design of the compression chamber was unoptimized for the required throughput, leading to excessive pressure that could cause mechanical stress on the components. High-pressure build-up can result in inconsistent pellet quality, which may adversely affect the final product’s marketability. Therefore, addressing this issue was crucial for ensuring that the wood pellet machine could consistently provide a reliable output while maintaining high quality.
To tackle these challenges, the project team undertaken a thorough review of the wood pellet machine’s design, focusing particularly on the geometry of the compression chamber. This analysis led to the implementation of several modifications, including adjustments to the internal dimensions and contours to facilitate better flow of the biomass material. Additionally, enhancements were made to the machine’s feed system to ensure a steady and even supply of raw materials, thus alleviating pressure fluctuations within the chamber.
Material selection also played a pivotal role in resolving the high-pressure issues. Employing advanced alloys and composites for critical components, such as the die and roller, helped improve durability and resistance to wear under high-pressure conditions. This strategic choice not only increased the lifespan of the wood pellet machine but also contributed significantly to the operational reliability of the entire system.
Through these engineering modifications and material innovations, the project successfully mitigated the challenges associated with high-pressure build-up, ensuring the wood pellet machine operated effectively at the targeted production levels.
Analysis of Technical Problem-Solving Strategies
In examining various case studies related to the wood pellet machine project employing ring molds, it becomes imperative to identify the common technical challenges and the corresponding solutions implemented. A comparative analysis reveals recurring problems such as inconsistent pellet quality, machinery malfunction, and maintenance challenges, which oftentimes arise due to varying raw material qualities or machine wear and tear.
One prominent challenge is the variance in raw material composition, which affects the density and moisture content of the pellets. Different pelletizing materials can lead to efficiency issues within the wood pellet machine. In response, several projects adopted a standardized material management and testing procedure, enabling more consistent inputs for the pelletizing process. Such strategies not only improved pellet quality but also optimized the machine’s performance.
Another technical hurdle identified was machine downtime caused by component failure. To mitigate this risk, projects emphasized predictive maintenance strategies leveraging IoT technologies. By integrating sensors that monitored machine performance and equipment wear in real-time, they were able to schedule timely maintenance. This proactive approach significantly reduced unplanned outages and extended the lifespan of the wood pellet machine.
Additionally, variations in production throughput were addressed by implementing adjustable operating parameters and refining the mold design for enhanced flow and extrusion rates. This flexibility allowed operators to adapt to different production scales and types of feedstock. Best practices from these cases underline the importance of continuous training and development for operators to ensure they’re equipped with the skills needed to resolve issues swiftly.
The lessons extracted from these wood pellet machine project cases not only highlight the necessity for adaptability and innovation in problem-solving but also underscore a collaborative approach that fosters knowledge sharing among teams. Each project contributes to a growing repository of strategies that can guide future endeavors in overcoming technical challenges effectively.
Best Practices for Ring Mold Pelletizing
To ensure optimal performance of wood pellet machines utilizing ring molds, it is essential to adhere to established best practices that address both operational efficiency and equipment longevity. Firstly, operators should regularly monitor the moisture content of the raw materials used in the pelletizing process. Ideally, the moisture level should range between 10% and 15% for optimal binding and pellet formation. Excess moisture can lead to poor pellet quality, while insufficient moisture may result in equipment wear and tear.
Moreover, it is advisable to maintain a consistent feed rate into the wood pellet machine. An irregular feed can cause fluctuations in pressure within the ring mold, leading to inconsistencies in pellet density and size. Regular calibration of the feed system should be performed to ensure that the material is fed steadily. In this regard, automation systems paired with sensors can significantly enhance the feed accuracy, thus optimizing the overall operation.
Maintenance schedules are equally crucial in prolonging the life of the ring molds and the wood pellet machines. It is recommended to inspect the ring molds and associated components regularly to identify any signs of wear or damage. This proactive measure can prevent costly downtime due to unexpected failures. Additionally, lubricating moving parts and cleaning the ring molds according to the manufacturer’s guidelines can greatly enhance performance and efficiency.
Finally, conducting regular assessments of equipment performance will help identify any emerging technical challenges early on. Utilizing data analytics to track production rates, pellet quality, and equipment operating conditions can inform necessary adjustments and improvements. Implementing these best practices for ring mold pelletizing not only mitigates potential risks but also enhances productivity, ensuring a seamless operation of wood pellet machines.
Future Directions in Wood Pellet Machinery
As the demand for sustainable energy sources continues to grow, the wood pellet industry is poised for significant advancements, particularly in the area of machinery that utilizes ring molds. The wood pellet machine has seen remarkable improvements in technology, with a strong focus on enhancing efficiency and production capabilities. Emerging trends suggest a move towards more automated and intelligent systems, which could revolutionize the manufacturing process of wood pellets.
One of the key areas of innovation involves the integration of artificial intelligence (AI) and machine learning algorithms into wood pellet machines. These technologies can optimize operational efficiency by monitoring and adjusting variables in real-time, such as temperature and pressure during the pelleting process. Such advancements not only aim to enhance product quality but also increase the overall yield of wood pellets, thereby reducing waste and operational costs.
In addition to AI, there is a growing emphasis on the development of advanced materials for ring molds used in wood pellet machinery. Increased wear resistance and thermal stability are crucial for improving the durability of these components. Future advancements may introduce novel composites or coatings that extend the lifespan of ring molds, thus enhancing the overall efficiency of the wood pellet machine. However, these developments are not without challenges. The industry must grapple with rising material costs and the necessity for thorough testing to ensure that new materials perform to the required standards.
Furthermore, as regulations around sustainability tighten, wood pellet machines will need to adapt to meet stricter environmental guidelines. Emerging technologies that promote energy efficiency and reduce emissions are likely to be a focal point for innovation. The industry must remain agile, anticipating potential disruptions while fostering an environment conducive to creativity and effectiveness in problem-solving.
Conclusion
Throughout the examination of various case studies concerning the operation of wood pellet machines utilizing ring molds, several critical insights have been gained. The operational efficiency of wood pellet machines is largely dependent on addressing the various technical challenges that arise during their use. These challenges include issues related to material feed consistency, moisture content, die wear, and machine maintenance. Effective problem-solving strategies are essential not only for overcoming these obstacles but also for ensuring high-quality pellet production.
One of the primary themes highlighted in the analysis is the importance of understanding the unique specifications and requirements dictated by the type of biomass materials being processed. Different raw materials exhibit varying characteristics, which can significantly influence the performance of wood pellet machines. For instance, softer materials may require a different approach than denser biomass. Responding to these characteristics through tailored operational strategies can enhance productivity and extend machine longevity.
Additionally, the case studies underscore the necessity of routine maintenance and monitoring of the wood pellet machines. Regular checks and prompt interventions can prevent minor issues from escalating into major disruptions, ensuring a smooth and efficient production process. Furthermore, engaging with advancements in technology can facilitate the development of more efficient pellet production methods.
In essence, the success of wood pellet machine projects hinges on a proactive approach to problem-solving and maintenance. By applying the lessons learned from the analyzed case studies, businesses can enhance operational outcomes and improve the quality of produced pellets. The highlighted strategies not only contribute to operational efficiency but also support sustainability goals in the biomass energy sector. Related: https://www.richimanufacture.com/2t-wood-pellet-plant-in-romania/