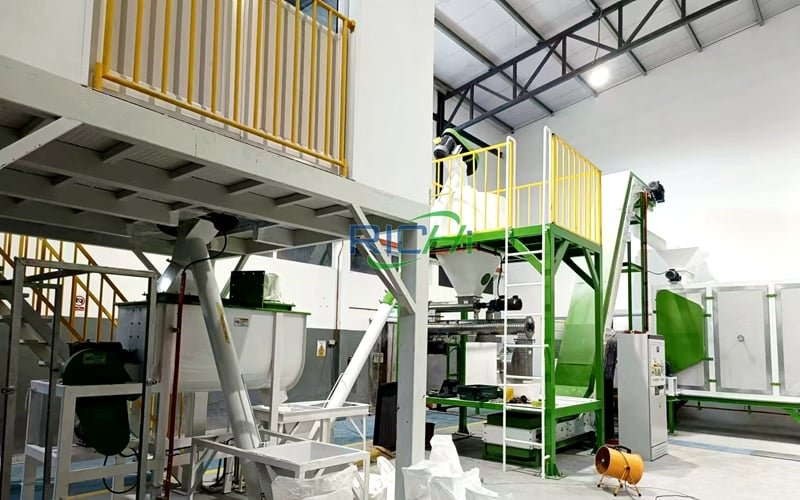
Introduction to Cat Litter Production Lines
Cat litter production lines play a crucial role in the manufacturing of various types of litter products, catering to the needs of pet owners and ensuring the comfort of their feline companions. These production lines typically operate within a capacity range of 1 to 2 tons per hour, which strikes a balance between efficiency and the flexibility to accommodate diverse production demands. The efficiency of a cat litter production line directly influences both the throughput and quality of the end products, establishing a critical factor for manufacturers keen on maintaining competitive advantage in the market.
The growing demand for cat litter has prompted manufacturers to invest in optimized production lines that can handle a range of materials, such as clumping clay, natural litter, and recycled products. Each material requires unique handling processes and equipment configurations, highlighting the need for tailored solutions. As the industry evolves, there is a marked emphasis on adopting advanced technologies that enhance production efficiency, reduce waste, and improve product quality. These advancements are vital for strengthening operational efficiency and meeting the ever-changing preferences of consumers.
Quality assurance remains a significant aspect of cat litter production, with manufacturers striving to produce litter that is safe, absorbent, and environmentally friendly. Continuous refinement of production processes and adherence to industry standards ensures that the final products meet customer expectations and regulatory requirements. Streamlining operations not only facilitates smoother production but also contributes to lower operational costs through reduced downtime and optimized resource allocation.
In this blog post, we will delve into several project case studies that illustrate common challenges encountered across cat litter production lines and the innovative solutions implemented to overcome them. By examining these cases, we aim to shed light on best practices within the industry, ultimately elevating the standards of cat litter manufacturing.
Overview of Project Cases
In the realm of cat litter production, various case studies illustrate the diversity and complexity of operations involved in the manufacture of different types of cat litter. These projects not only showcase the wide array of products that can be developed but also highlight the specific requirements and challenges faced by manufacturers in each scenario. By examining these project cases, we gain valuable insights into the operational nuances associated with a cat litter production line.
One notable case involved a manufacturer specializing in clumping clay cat litter. This project was initiated to improve the existing production line efficiency, requiring a significant upgrade to both the machinery and the workflow. The specific requirements encompassed higher throughput while maintaining quality standards for clumping ability and odor control. By addressing these challenges, the production line was ultimately optimized to produce a superior product with reduced energy consumption and waste.
Another case focused on biodegradable cat litter made from recycled paper. This project aimed to cater to environmentally conscious consumers while facing the challenge of sourcing sustainable materials. The requirement was to create an efficient cat litter production line that could handle varying particle sizes and moisture content found in the raw materials. This necessitated innovations in preprocessing techniques and machinery design to ensure that the final product met user expectations effectively.
Additionally, a project centered around crystal cat litter presented unique challenges related to the production process. The focus here was on achieving a balance between absorbency and dust control, while also ensuring consistency across batches. Key parameters specified included the need for precise temperature control during the manufacturing process and advanced packaging solutions to maintain product integrity during distribution. Each of these cases underscores the distinct operational requirements and objectives inherent in different cat litter production lines.
Program Design Challenges
The design of a cat litter production line encompasses a variety of complexities that can significantly impact its efficiency and output quality. One of the primary challenges faced by manufacturers is the identification and rectification of common design flaws. These issues can arise from improper configuration of equipment, inadequate flow of materials, or insufficient integration of automation technologies. When these design concerns are not addressed, they can lead to production bottlenecks, increased waste, and ultimately, higher operational costs.
Another critical consideration in the design of a cat litter production line is scalability. As demand for various types of cat litter evolves, production lines must be adaptable to accommodate changes without requiring a complete overhaul. This necessitates a modular approach to design, allowing manufacturers to incorporate additional machinery or make modifications as needed. Flexibility in production processes can lead to enhanced productivity and responsiveness to market changes.
Customizing the production line design to meet specific client needs is also paramount. Each client may have unique requirements regarding the type of cat litter being produced, the scale of operations, and even environmental considerations. For instance, clients focused on eco-friendly products may require modifications in the manufacturing process to support the use of biodegradable materials. Therefore, an effective design process involves thorough consultations with clients to understand their individual requirements, which in turn informs the creation of a bespoke production line that optimally aligns with their goals.
Ultimately, recognizing and addressing these program design challenges in the cat litter production line can play a vital role in ensuring operational efficiency and product quality. By carefully considering design flaws, scalability, and customization, manufacturers can create production lines that not only meet current market demands but are also equipped to adapt to future changes.
Site Logistics and Layout Problems
Effective site logistics and layout are critical components in the optimal functioning of a cat litter production line. These elements directly influence production efficiency, operational costs, and the overall workflow within a facility. One common challenge is space optimization. Often, production facilities are constrained by limited space, making it difficult to fit all necessary equipment, storage, and operational areas without compromising accessibility and safety. Insufficient space can lead to bottlenecks, where the movement of materials is hampered, delaying production timelines and increasing operational costs.
Another significant factor to consider is workflow efficiency. The physical arrangement of equipment and personnel plays a vital role in determining how smoothly materials and products move through various stages of the production process. Poorly designed layouts can lead to excessive travel distances for workers, lengthy material handling times, and an increase in the risk of accidents. A production line designed with a linear flow in mind, where each step logically follows the previous one, tends to reduce unnecessary movements and enhance productivity.
Site conditions, such as floor space, ceiling height, and proximity to loading docks, also impact the placement of machinery and equipment in a cat litter production line. For example, if the layout does not consider the required height for machinery installation, it could result in modifications that are expensive and time-consuming. Similarly, factors such as ventilation and access to utilities must be meticulously planned to prevent future operational problems.
Solutions to these spatial problems can include implementing modular designs that allow for flexibility in the layout as needs change over time. Furthermore, leveraging advanced technologies, such as warehouse management systems, can assist in optimizing facility layout based on real-time data. In conclusion, addressing site logistics and layout problems is essential for ensuring functional efficiency and achieving production goals in any cat litter production line.
Equipment Challenges and Considerations
The selection of appropriate equipment is a critical aspect of operating an effective cat litter production line. Given the diversity of cat litter types—ranging from clay-based to biodegradable materials—manufacturers must carefully evaluate machinery options to ensure compatibility and efficiency. Key equipment includes mixers, crushers, screens, and packaging machines, each serving a specific function within the production process. The integration of advanced automation technology further enhances these operations, facilitating faster production rates and reduced labor costs.
Installation challenges often arise during the setup phase of a cat litter production line. Proper calibration and alignment of machinery are essential to prevent operational inefficiencies. A misaligned conveyor system, for instance, can lead to material spillage or uneven distribution, which subsequently affects the overall quality of the final product. Furthermore, assessing floor space and utility requirements is crucial to accommodate the machinery without hampering workflow. Regular maintenance schedules should also be established to mitigate equipment failures, which can result in costly downtime and interruptions in production.
Common equipment failures in the cat litter production line may include issues such as mechanical wear, electrical malfunctions, and software glitches. For example, a malfunctioning packaging machine can lead to incorrect bag weights or improperly sealed products, thus affecting marketability. To combat these challenges, manufacturers are encouraged to opt for high-quality equipment and invest in training for their personnel on proper operation and troubleshooting techniques.
Ultimately, selecting the RICHI cat litter making machine for a cat litter production line is not just about meeting immediate operational demands but also about establishing a reliable and efficient production environment that can adapt to future needs. By addressing these equipment challenges proactively, manufacturers can enhance output while ensuring that they meet the unique requirements of their specific projects.
Installation and Commissioning Issues
The installation and commissioning phase of a cat litter production line is a critical component in ensuring the success of the overall operation. During this phase, various challenges can arise, often stemming from insufficient coordination among different teams involved in the process. Each team, ranging from project managers to equipment suppliers, must collaborate effectively to adhere to the established timelines and protocols, otherwise, inefficiencies could arise that impede the project’s success.
One of the primary issues faced during the installation phase is a lack of clear communication among the involved parties. It is essential to establish a comprehensive communication plan that outlines the roles and responsibilities of each team, along with a timeline for key milestones. If communication remains fragmented, delays may occur, leading to increased costs and a longer installation timeline. Regular meetings and updates can facilitate better coordination and allow for quick identification of any bottlenecks that may hinder progress.
Moreover, adhering to a strict timeline is crucial for the timely commissioning of the cat litter production line. Delays might not only postpone the start of production but also affect equipment warranty and operational efficiency. One effective approach to maintaining adherence to timelines is to utilize project management tools that track progress and identify potential delays before they become significant issues. Such tools enable teams to allocate resources efficiently and keep all stakeholders informed.
During the commissioning phase, implementing standard protocols is vital to ensure that all equipment functions correctly and meets operational requirements. Performing pre-commissioning checks, regular maintenance, and ensuring compliance with safety regulations can help mitigate the risk of future malfunctions. By adopting best practices, this phase can go smoothly, resulting in an efficient and functional cat litter production line.
After-Sales Challenges and Solutions
After-sales support is a critical aspect of any manufacturing process, particularly in specialized fields such as cat litter production line systems. The complexities inherent in the operation of these production lines necessitate a robust framework for addressing various challenges that clients may encounter post-installation. These challenges can include maintenance issues, parts replacements, technical support, and operator training, all of which are vital for ensuring optimal performance and longevity of the equipment.
Maintenance is one of the primary after-sales concerns in cat litter production lines. Regular servicing can prevent breakdowns and enhance productivity. Manufacturers should offer comprehensive maintenance packages that not only address routine check-ups but also provide emergency repairs. This proactive approach can significantly reduce downtime and maintain the operational efficiency of the production line.
Another crucial aspect is parts replacement. Given the constant wear and tear of machinery, it is essential for clients to have access to high-quality replacement parts that are compatible with their specific production line configurations. Dealers should maintain an inventory of key components and establish a streamlined system for clients to order parts easily. Timely delivery of these components helps ensure that production schedules are not adversely affected.
Furthermore, technical support is indispensable in resolving any operational issues that may arise. By offering 24/7 customer service through various channels—such as phone, email, or live chat—manufacturers can significantly improve client satisfaction. Technicians with expertise in the specific nuances of cat litter production lines can provide valuable insights and solutions remotely.
Lastly, the training of operators is fundamental for minimizing errors and maximizing efficiency. Manufacturers should implement training programs tailored to different skill levels, helping clients’ staff to become proficient in running the production line effectively. Adequate training not only empowers operators but also fosters a culture of continuous improvement within organizations.
Custom Solutions by Richi Machinery
Richi Machinery stands out in the field of cat litter production line development by emphasizing tailor-made solutions that address the unique needs of each client. Understanding that no two production environments are identical, Richi Machinery invests time and resources to conduct thorough assessments of customer requirements. This commitment to customization enables the company to deliver highly efficient and effective systems that optimize both production processes and operational efficiency.
The approach begins with an in-depth analysis of a client’s specific situation, including the types of cat litter products to be produced, the required volume of output, and any particular quality standards that must be met. By engaging in comprehensive consultations, Richi Machinery identifies challenges and opportunities that may influence the design and functionality of the cat litter production line. This is vital for ensuring that all elements of the production process—from raw material handling to final packaging—are integrated seamlessly.
After the initial assessment, Richi Machinery develops a customized solution that incorporates advanced technologies and innovative designs tailored to the client’s unique operational context. This may include automation features, energy-efficient machinery, or specialized equipment designed for specific litter types. The emphasis on bespoke solutions not only addresses the immediate needs of clients but also provides scalability for future growth, thereby enhancing long-term operational success.
Furthermore, ongoing support and maintenance services are part of Richi Machinery’s commitment to its clients. By fostering a partnership that extends beyond the installation phase, the company ensures that clients can adapt and evolve their production lines in response to changing market demands. Overall, Richi Machinery’s tailored approach plays a crucial role in maximizing the performance of cat litter production lines, ultimately leading to improved profitability and business sustainability.
Future Trends in Cat Litter Production Technology
As the market for cat litter evolves, several future trends are shaping the landscape of cat litter production lines. One of the primary advancements lies in automation technology. The integration of robotics and smart systems into production line operations offers increased efficiency, reduced labor costs, and enhanced product consistency. Automated systems can provide real-time data analysis, enabling manufacturers to adjust processes dynamically and respond to varying demand levels, ultimately increasing the competitiveness of their operations.
Another significant trend is the push towards environmental sustainability. With consumers becoming more conscious of their ecological footprint, manufacturers are increasingly exploring eco-friendly materials for cat litter. This includes the utilization of renewable resources such as corn, wheat, and recycled paper. Moreover, innovations in biodegradable litter options demonstrate a growing commitment to reducing plastic waste. Cat litter production lines will likely incorporate these sustainable practices not only to meet consumer demand but also as a way to adhere to regulatory standards aimed at minimizing environmental impact.
Advances in material sciences are also poised to transform cat litter production. Research into novel absorbent materials promises to improve product performance by enhancing clumping abilities, odor control, and overall absorbency. For instance, the development of advanced clumping agents could lead to more effective litter that diminishes the need for frequent changes, appealing to both pet owners and manufacturers seeking operational efficiencies. By leveraging cutting-edge materials, production lines can produce a range of specialized products catering to different feline needs, thus expanding market opportunities.
In conclusion, the future of cat litter production lines appears promising, with a blend of automation, sustainable practices, and innovative materials set to drive the industry forward. These trends not only respond to consumer preferences but also pave the way for a more efficient and environmentally aware production process, essential for meeting the challenges of tomorrow.
Conclusion and Final Thoughts
In conclusion, the journey through the intricacies of cat litter production lines reveals the multifaceted challenges and solutions inherent in this industry. As highlighted throughout the blog post, the demand for innovative, efficient production methods is crucial not only for optimizing manufacturing processes but also for meeting the evolving preferences of consumers. The case studies presented demonstrate that adapting to technological advancements and maintaining product quality are paramount for success in the cat litter market.
Moreover, it is essential to address common challenges, such as waste management and the variability of raw materials, which can significantly impact the overall efficiency of a cat litter production line. Understanding these challenges allows manufacturers to implement targeted solutions and reduce operational costs while ensuring that product standards are met. This focus on efficiency and reliability is where partnerships with experienced machinery manufacturers, such as Richi Machinery, become invaluable.
Richi Machinery offers a range of practical solutions tailored to the needs of cat litter production, including state-of-the-art machinery and operational support. By integrating modern technology and innovative design, companies can ensure their production lines achieve a high output, thus meeting market demand effectively. Client satisfaction is enhanced as the solutions provided not only improve production efficiency but also contribute to a sustainable practice in the industry.
In summary, navigating the cat litter production landscape requires a comprehensive approach that considers both the challenges faced and the solutions available. With the right tools and expertise, companies can optimize their production lines, driving both efficiency and satisfaction in a dynamic market environment. Investing in quality machinery and processes will undoubtedly position manufacturers for long-term success in the ever-growing pet care industry.