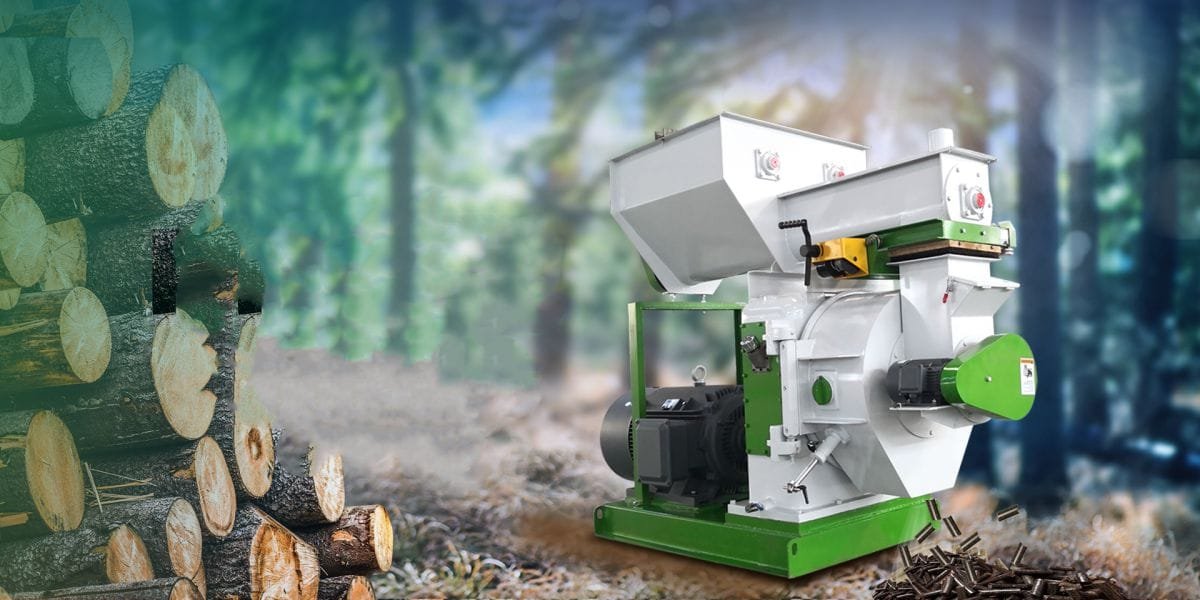
Wood pelletizer machines are crucial in the biomass industry, transforming wood chips, sawdust, and agricultural residues into high-density pellets used for energy production, animal bedding, and other applications. To achieve optimal efficiency and maintain stable operation, it’s essential to implement proper maintenance practices, continuously monitor performance, and make necessary adjustments. This guide outlines key strategies to ensure the stable operation of a wood pelletizer machine.
1. Regular Maintenance
Regular maintenance is the cornerstone of keeping a wood pelletizer machine running smoothly. A well-maintained machine is less likely to experience unexpected breakdowns and can consistently operate at peak efficiency.
- Scheduled Inspections: Develop a routine inspection schedule to examine critical components such as the pellet die, rollers, bearings, and gearbox. Regular checks can identify wear and tear early, preventing more significant issues down the line.
- Lubrication: Ensure that all moving parts are properly lubricated according to the manufacturer’s guidelines. Adequate lubrication minimizes friction, prevents overheating, and extends the life of machine components.
- Cleaning: Regularly clean the machine to remove dust, debris, and residual materials. This practice prevents blockages and ensures efficient operation. Pay special attention to the die and rollers, as buildup in these areas can degrade pellet quality.
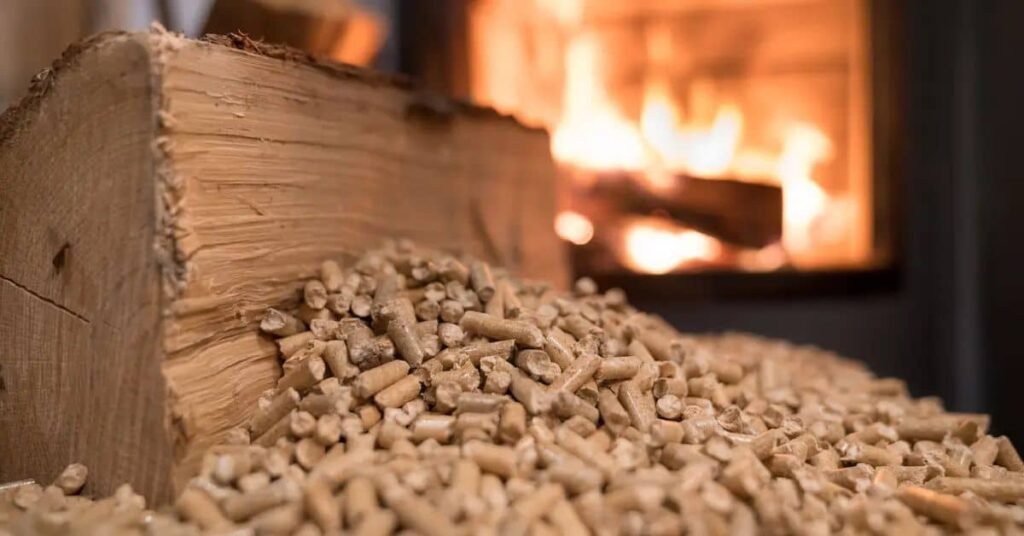
2. Monitor Raw Material Quality
The quality of the raw materials fed into the wood pellet press machine directly impacts the machine’s performance and the final product.
- Moisture Content: Keep a close eye on the moisture content of the raw materials. The ideal range for wood pellet production is 10% to 15% moisture. Too much moisture can lead to poor pellet formation and increased wear on the machine.
- Material Consistency: Ensure that raw materials are uniform in size and composition. Inconsistent material can cause feeding issues and affect pellet quality. Consider using a hammer mill to grind larger pieces into a uniform size before feeding them into the pelletizer.
3. Optimize Operating Conditions
Operating conditions play a significant role in the stability and efficiency of a wood pelletizer machine.
- Temperature Control: Monitor the machine’s temperature during operation. Excessive heat can damage components and compromise pellet quality. Ensure the cooling system is working correctly to maintain optimal temperatures.
- Pressure Settings: Adjust the pressure settings of the rollers and die to achieve proper compression of the raw materials. Incorrect pressure can result in poorly formed pellets or excessive wear and potential machine damage.
- Feeding Rate: Maintain a consistent feeding rate to avoid overloading or underfeeding the machine. An uneven feed can cause pressure and temperature fluctuations, leading to instability in pellet production.
4. Train Operators
Proper training is essential for operators to maintain the stable operation of a wood pelletizer machine.
- Operational Training: Provide thorough training on machine operation, including starting and stopping procedures, setting adjustments, and performance monitoring. Operators should understand the importance of consistent feeding rates and maintaining raw material quality.
- Safety Protocols: Train operators on safety protocols to minimize the risk of accidents and injuries. This includes the correct use of personal protective equipment (PPE) and knowledge of emergency shutdown procedures.
- Maintenance Procedures: Educate operators on routine maintenance tasks, such as lubrication and cleaning, so they can perform these tasks effectively and recognize when professional maintenance is needed.
5. Implement Monitoring Systems
Monitoring systems are invaluable for maintaining the stable operation of a wood pelletizer machine by providing real-time performance data.
- Performance Metrics: Utilize monitoring systems to track key performance metrics, including production rates, energy consumption, and temperature. Analyzing this data can help identify trends and potential issues before they escalate.
- Automated Alerts: Consider implementing automated alert systems to notify operators of any deviations from normal operating conditions. Quick intervention can prevent issues and maintain operational stability.
6. Keep Spare Parts on Hand
Having spare parts readily available can minimize downtime in case of component failure.
- Critical Components: Identify critical components prone to wear, such as the die, rollers, and bearings. Keep a stock of these parts on hand to enable quick replacements when necessary.
- Supplier Relationships: Build strong relationships with reliable suppliers to ensure that replacement parts can be sourced quickly and efficiently, reducing the risk of extended downtime due to waiting for parts.
7. Document Maintenance Activities
Thorough documentation of maintenance activities is essential for ensuring the long-term stability of the wood pelletizer machine.
- Maintenance Logs: Maintain detailed logs of all inspections, maintenance tasks, and part replacements. This documentation can help identify patterns in wear and inform future maintenance decisions.
- Performance Records: Keep records of performance metrics over time to monitor changes and spot potential issues. Analyzing this data can lead to optimized operating conditions and improved efficiency.
Conclusion
Ensuring the stable operation of a wood pelletizer machine involves a combination of regular maintenance, monitoring raw material quality, optimizing operating conditions, training operators, implementing monitoring systems, keeping spare parts on hand, and documenting maintenance activities. Focusing on these areas will enhance the efficiency and longevity of the machine, resulting in better pellet quality and lower operational costs.
As the demand for renewable energy continues to grow, maintaining a well-functioning wood pelletizer machine will be crucial for success in the biomass industry. By investing in proper maintenance and operational practices, businesses can ensure that their pellet production processes are efficient, reliable, and sustainable.