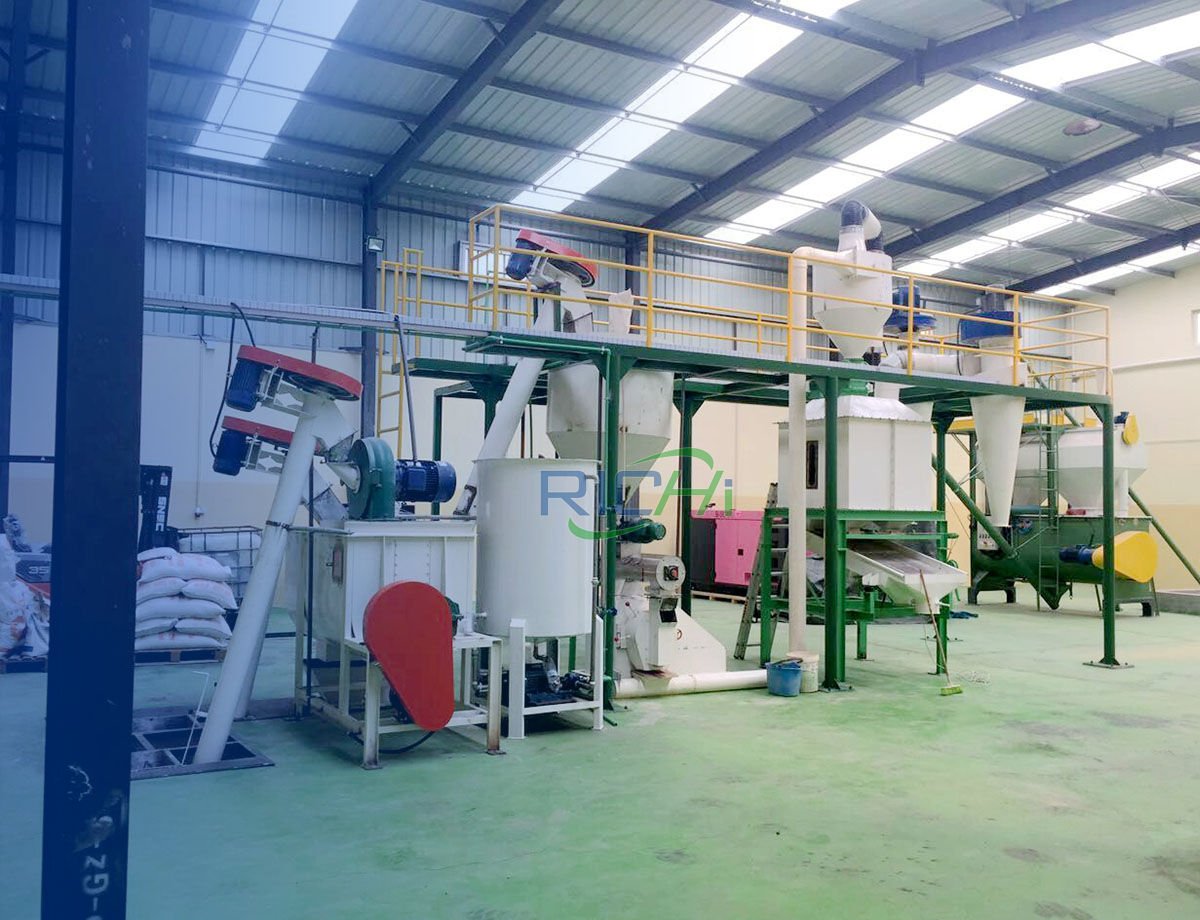
The animal feed industry plays a crucial role in the agricultural sector, providing essential nutrition to livestock and poultry. As the demand for high-quality animal feed continues to rise, the efficiency of feed manufacturing processes becomes increasingly important. Small feed factory machines, particularly those with production capacities of around 3-4 tons per hour, are widely used in this industry. Understanding how the production efficiency of these machines influences total costs is vital for feed manufacturers looking to optimize their operations and improve profitability. This article explores the relationship between production efficiency and total costs in small feed factories.
1. Understanding Production Efficiency
Production efficiency refers to the ability of a feed manufacturing machine to convert raw materials into finished products with minimal waste and maximum output. In the context of small feed factory machines, several factors contribute to production efficiency:
- Operational Speed: The speed at which the machine operates directly impacts the volume of feed produced within a given timeframe. A higher operational speed generally leads to increased output, which can reduce the cost per ton of feed produced.
- Energy Consumption: Efficient machines consume less energy while maintaining high production rates. Energy costs are a significant portion of total production costs, so machines that operate efficiently can lead to substantial savings.
- Material Utilization: The ability of the machine to effectively process raw materials without excessive waste is critical. High material utilization rates mean that more of the input materials are converted into finished feed, reducing overall costs.
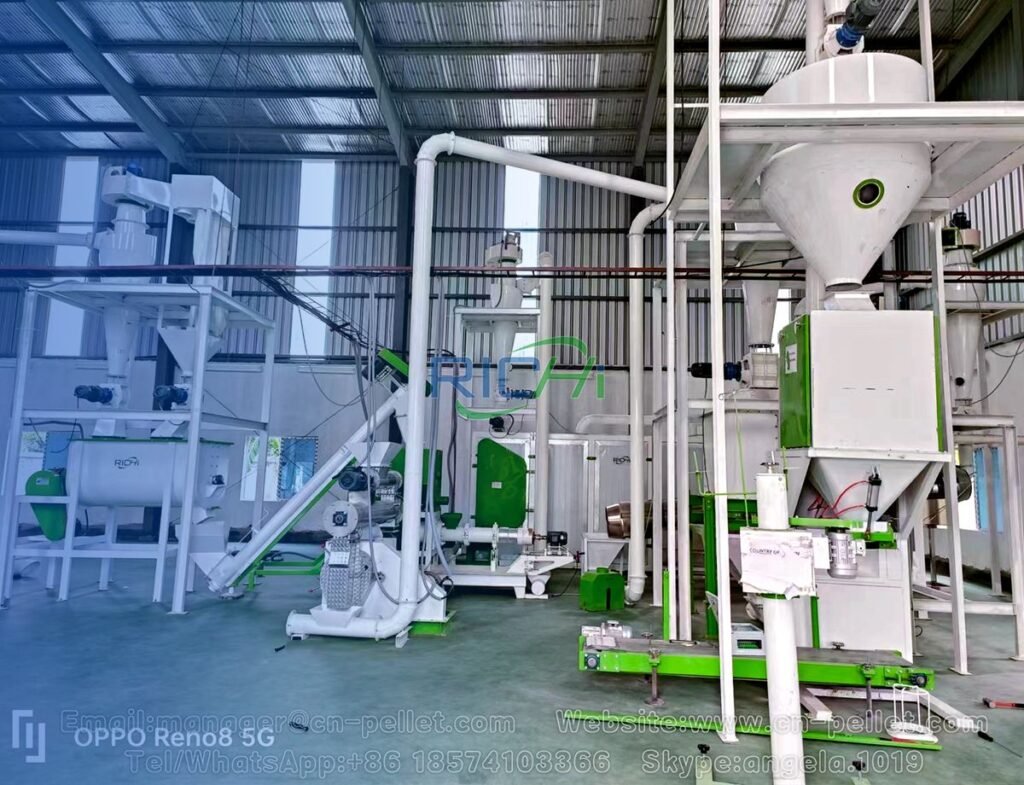
2. Impact on Direct Costs
The production efficiency of small feed factory machines directly affects various direct costs associated with feed manufacturing.
- Raw Material Costs: Efficient machines maximize the conversion of raw materials into finished products, which means less waste. By minimizing waste, manufacturers can lower their raw material costs, as they are able to produce more feed from the same quantity of inputs.
- Energy Costs: Energy consumption is one of the largest expenses in feed production. Machines that operate efficiently can significantly reduce energy costs. For instance, if a machine uses 30% less energy than a less efficient model, the savings can be substantial over time, directly impacting the total cost of production.
- Labor Costs: The efficiency of production processes can also influence labor costs. Machines that require less manual intervention or have automated features can reduce the number of workers needed on the production line. This reduction in labor can lead to lower overall labor costs, contributing to cost savings. (Related post: small feed making machine)
3. Influence on Indirect Costs
In addition to direct costs, production efficiency can also impact various indirect costs associated with operating a small feed factory.
- Maintenance Costs: Efficient machines tend to have lower maintenance costs. When machines operate smoothly and consistently, the wear and tear on components is minimized, leading to fewer breakdowns and repairs. This reduction in maintenance needs can significantly lower indirect costs over time.
- Downtime Costs: Production efficiency directly affects the amount of downtime experienced by the machine. Inefficient machines may require more frequent repairs or adjustments, leading to increased downtime. Each hour of downtime can result in lost production and revenue, making it essential to invest in machines that operate efficiently.
- Quality Control Costs: Higher production efficiency often correlates with improved product quality. Efficient machines produce consistent feed pellets with fewer defects, reducing the need for rework or quality control measures. This can lead to lower costs associated with quality assurance and customer complaints.
4. Long-Term Financial Implications
Investing in small feed factory machines that offer high production efficiency can have significant long-term financial implications for feed manufacturers.
- Return on Investment (ROI): Machines that operate efficiently can provide a quicker return on investment. Lower operational costs, combined with higher output, can lead to increased profitability. Manufacturers can recoup their initial investment more rapidly when production efficiency is prioritized.
- Scalability: Efficient machines allow for easier scalability. As demand for animal feed increases, manufacturers can ramp up production without needing to invest in additional equipment. This flexibility can lead to increased market competitiveness and profitability.
- Sustainability: In today’s market, sustainability is becoming increasingly important. Efficient machines that minimize waste and energy consumption contribute to more sustainable production practices. This can enhance a company’s reputation and appeal to environmentally conscious consumers.
5. Conclusion
The production efficiency of small feed factory machines significantly impacts total costs in animal feed manufacturing. By maximizing operational speed, minimizing energy consumption, and ensuring effective material utilization, manufacturers can reduce direct costs associated with raw materials, energy, and labor. Additionally, improved efficiency can lower indirect costs related to maintenance, downtime, and quality control.Investing in high-efficiency feed manufacturing equipment is essential for feed producers looking to enhance profitability and sustainability.
As the demand for high-quality animal feed continues to rise, prioritizing production efficiency will be crucial for success in this competitive industry. By understanding the relationship between production efficiency and total costs, manufacturers can make informed decisions that contribute to their long-term success and growth in the animal feed market.
For details please contact: pellet mill machine
WhatsApp:86 138 3838 9622
Email:enquiry@richipelletmachine.com