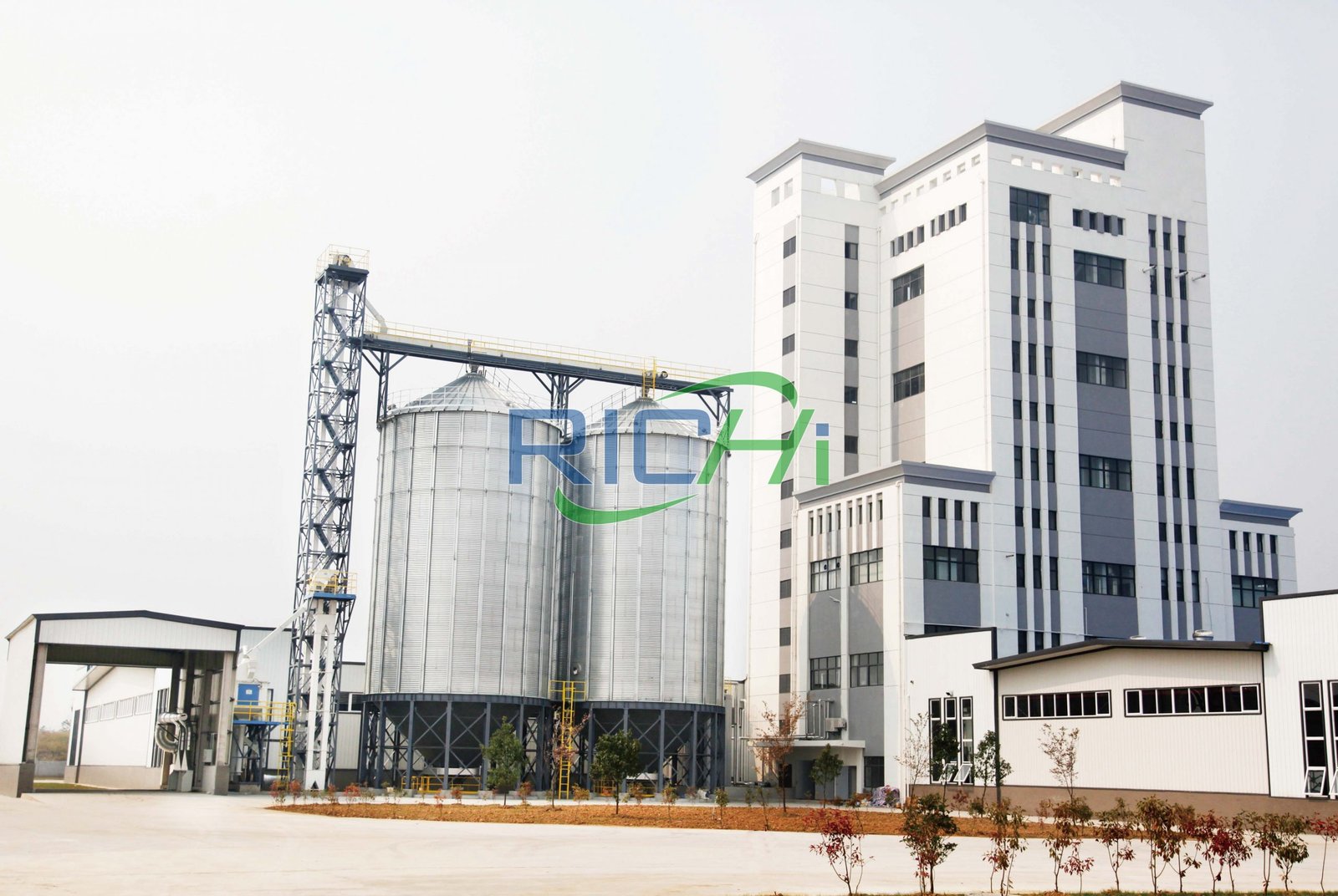
Animal feed factory project is usually selected according to the production scale, production varieties and production process. Therefore, different feed factories often use different equipment. However, some basic equipment of feed processing are the same. According to the process flow, they generally include raw material receiving and cleaning equipment, batching equipment, mixing equipment, crushing equipment, granulation equipment, expansion equipment, liquid spraying equipment, packaging equipment, conveying equipment, ventilation and dust removal equipment and central control system.
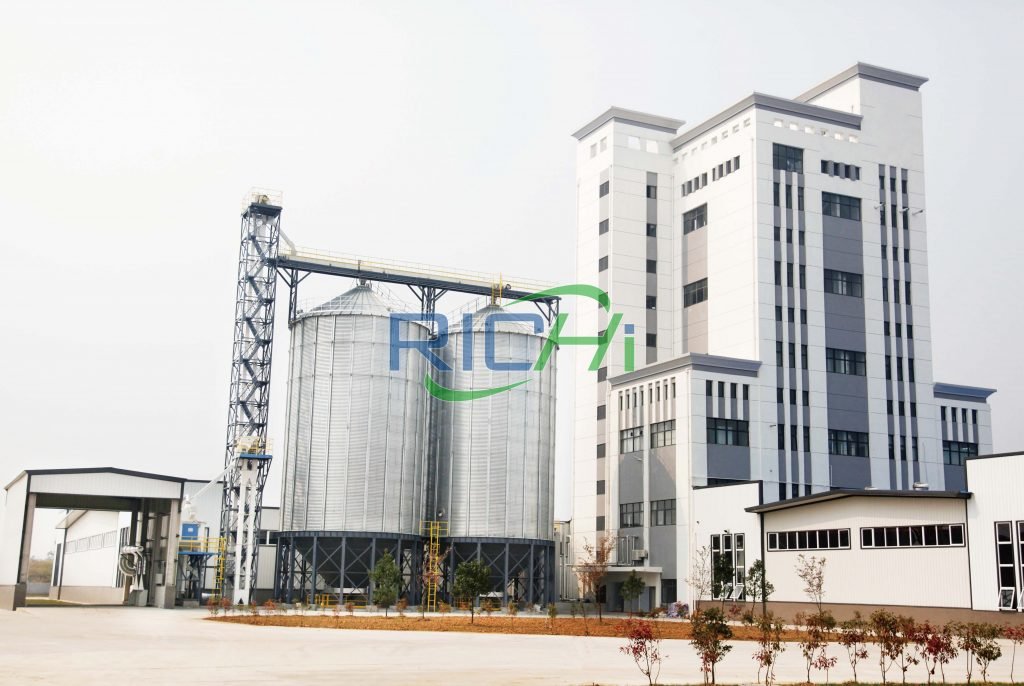
1. Raw material cleaning
Received bulk raw materials corn and soybean meal. The cleaning process is all the work units that put the corn and soybean meal that have passed the inspection of the raw material inspector into the silo. In this process, the impurities in the raw materials are first removed by the impurity removal equipment, and then transported to the silo through the receiving equipment and demagnetization equipment as planned.
2. Batching process
The batching process is to weigh the raw materials in the batching bin from the feeder under each batching bin according to the formula requirements. After each raw material is weighed by the batching scale, it is transported to the powder storage bin. The ingredients are weighed out from the silo, and these weighed raw materials enter the powder silo. A small amount of materials and premixes are added and directly weighed manually before being put into the silo for mixing. The quality of batching process directly affects the accuracy of product batching.
3. Crushing process
Crushing process refers to that the raw materials to be crushed in the silo are sent to the crusher for pulverization, and then sent to the silo for mixing by the conveyor. The purpose of this process is to control the particle size of the material. The design efficiency of the crusher in this process determines the capacity of this process equipment, and is also the process with the largest energy consumption in the production of powdery materials.
In addition, it is worth mentioning that crushing large hard particles so that the large particles become small broken particles can make the hardness of the particles significantly reduced. By crushing large pellets, the internal structure of the pellets is destroyed, which reduces the pressure-bearing capacity of the pellets and reduces their hardness.
4. Mixing process
In the mixing process, various crushed raw materials are discharged into the mixer from the mixing bin, and oil is added to the feed in the mixer through the liquid adding system according to the needs, so that the components are evenly mixed and the desired mixing effect is achieved. The material discharged from the mixer is the finished product, which is directly sent to the packaging process of the finished product for packaging and delivery. When producing pellet feed, the mixed powder is sent to the silo for granulation. In order to ensure the efficiency of the mixer, the maintenance personnel must regularly check and maintain the equipment and regularly test the efficiency of the mixer.
5. Granulation process
The mixed materials are sent to the compression chamber of the granulator after conditioning from the granulator bin and compressed into pellet feed. Cooled by a cooler and screened by a screening device to obtain standard particles. During tempering, the steam quantity shall be adjusted according to the requirements of particle type. Ring mold (aperture, compression ratio, material, etc.) shall be selected according to the requirements of particle process quality. During cooling, the cooler shall be adjusted according to the variety, indoor temperature and humidity, season and other factors to reach the qualified particle temperature and humidity.
6. Expansion equipment
It can produce aquatic feeds with different densities such as floatability, sedimentation and diffuse sedimentation, and can also be used as raw materials to make starch lake and destroy anti nutritional factors in soybeans.
7. Dust removal equipment
This is the equipment to absorb dust and protect the environment. The air volume required for conveying dust is smaller than that for conveying materials. Their supporting equipment mainly includes: fans, pipes, dust collectors, fans and bag filters.
8. Spraying equipment
Before granulation, the fat content in the material should not be too large, otherwise it will be too loose to make a good granular material, so the added grease in the mixer should not exceed 3%. If there is more than 3% oil to be added in the feed formula, the excess part shall be sprayed on the surface of the pellet feed by post spraying after granulation. Some fat soluble vitamins will become ineffective due to ripening in the granulation process. They can also be dissolved in fat and added to pellet feed by spraying after use.
Post-ripening and post-spraying processes are less used in the production process of livestock and poultry feeds, but are more widely used in the production process of fish feeds and special aquatic feeds. Post-ripening can make the starch inside the pellet fully paste, so that the internal structure of the pellet is more dense and prevent the immersion of water, which is conducive to the stability of aquatic feed pellets in water, and also improve the hardness of the pellet.
Based on thousands of successful animal feed factory projects, RICHI Machinery can provide you with the best poultry feed factory cost and design scheme. We can customize the feed processing machinery according to your requirements for pellet size, hourly production capacity and different animals. It can be used to make animal feed for cattle, cattle, sheep, horses, pigs, rabbits, chickens, ducks and other animals. Experienced engineers are also available for installation guidance and training.
